Understanding Rotomolding: A Versatile Plastic Molding Process
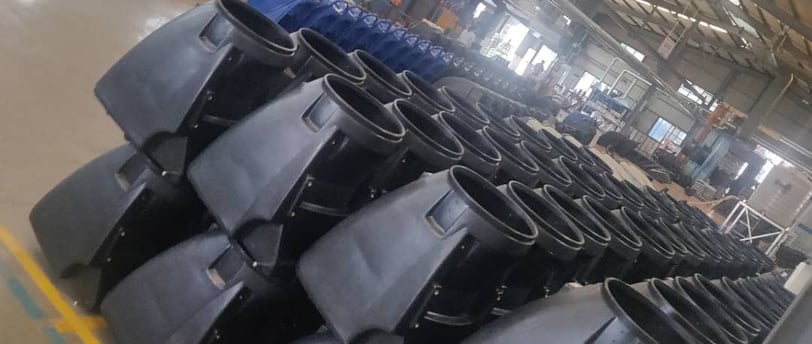
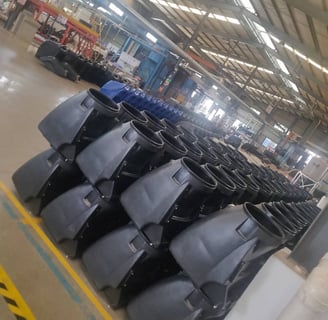
What is Rotomolding?
Rotomolding, or rotational molding, is a unique plastic molding process that utilizes heat and rotation to create hollow parts. This innovative technique has gained popularity in various industries due to its ability to produce large, durable products with efficiency. Whether it’s toys, tanks, or even surfboards, rotomolding is a plastic molding process designed to meet diverse needs.
The Rotomolding Process Explained
The rotomolding process begins with a mold, typically made of aluminum or steel. The chosen plastic material, often in the form of powdered resin, is loaded into the mold. As the mold rotates, it is heated evenly, allowing the plastic to melt and adhere to the interior surface of the mold. The rotation ensures that the plastic is applied evenly, creating a consistent wall thickness.
Once the desired thickness is achieved, the mold is cooled, causing the molten plastic to solidify. After cooling, the mold opens, and the final product is removed. This simple yet effective process allows manufacturers to produce complex shapes and large items without the risk of warping.
Applications and Advantages of Rotomolding
Rotomolding is renowned for its versatility, making it an ideal choice across various sectors, including automotive, marine, and recreational industries. For example, in the automotive industry, rotomolding creates durable parts resistant to impact and weathering. In marine applications, large tanks for storage or transport are efficiently produced with this method.
One of the primary advantages of rotomolding is its cost-effectiveness. The initial mold investment is typically lower than other plastic molding processes, making it ideal for medium to large production runs. Additionally, rotomolding allows for minimal waste, as the process can reuse scrap materials. It also supports a wide array of plastic materials, enabling manufacturers to select options that provide the best performance.
Moreover, rotomolding delivers consistent quality with customizable features, such as color, texture, and added functionalities. Manufacturers can enhance products with processes like foam filling, which improves insulation and buoyancy, making rotomolded products an excellent choice for outdoor equipment.
In summary, rotomolding is a dynamic and effective method for producing hollow plastic parts. Its applications span numerous industries, from automotive to marine, highlighting its versatility and cost-efficiency. Understanding this molding process is essential for manufacturers seeking innovative solutions to their plastic production needs.